In our increasingly connected world, we rely heavily on technology to power our daily lives. But what happens when that technology fails us? Enter the tech truck roll – a crucial component of the tech support ecosystem that often goes unnoticed until we need it most. Whether you’re a curious consumer or a business owner looking to optimize operations, understanding what a tech truck roll is can shed light on an essential aspect of our digital infrastructure.
Defining the Tech Truck Roll
A tech truck roll, at its core, is the dispatch of a technician to a customer’s location to resolve a technical issue that couldn’t be fixed remotely. It’s the cavalry charge of the tech world, swooping in when all other options have been exhausted. The term “truck roll” originates from the early days of telecommunications when service vehicles would literally roll out to address line issues.
In today’s landscape, a tech truck roll can encompass a wide range of services, from fixing a faulty internet connection to setting up complex business networks. It’s the human touch in an increasingly automated support structure, bringing expertise directly to your doorstep.
When Does a Tech Truck Roll Happen?
Not every tech hiccup warrants a truck roll. Here’s a quick rundown of common scenarios:
- Persistent internet outages
- Hardware failures that can’t be diagnosed remotely
- Initial installations of complex systems
- Security system malfunctions
- Major software issues affecting business operations
Before a truck rolls out, companies typically go through a rigorous triage process. This involves remote diagnostics, customer interviews, and attempts at guided self-repair. Only when these steps fail does the green light for a truck roll flash.
The Anatomy of a Tech Truck Roll
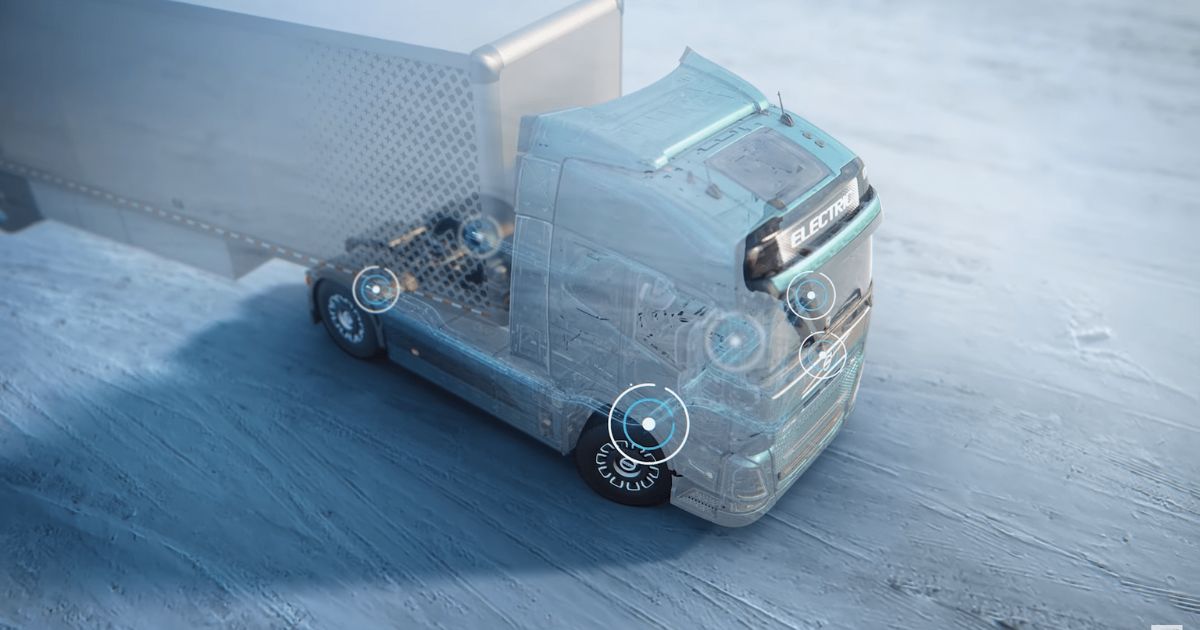
Who’s Behind the Wheel?
The unsung heroes of the tech truck roll are the technicians themselves. These aren’t your average Joes – they’re highly skilled professionals with a diverse set of certifications and expertise. Depending on the issue at hand, you might encounter:
- Network specialists
- Hardware repair experts
- Security system technicians
- Fiber optic specialists
Many of these pros hold certifications from industry giants like Cisco, CompTIA, or Microsoft. They’re the Swiss Army knives of the tech world, ready to tackle a myriad of issues with their knowledge and tool-laden trucks.
What’s in the Truck?
Speaking of tools, a tech truck is essentially a mobile workshop. Here’s a peek into what these rolling arsenals typically carry:
Category | Examples |
Diagnostic Tools | Multimeters, network analyzers, cable testers |
Repair Equipment | Soldering irons, replacement parts, crimping tools |
Safety Gear | Hard hats, safety glasses, gloves |
Documentation | Service manuals, wiring diagrams, tablet for digital resources |
Communication Devices | Smartphones, two-way radios |
This extensive array of equipment allows technicians to diagnose and solve a wide range of issues on the spot, minimizing the need for follow-up visits.
The Cost Factor: Why Tech Truck Rolls Matter
The phrase “time is money” takes on new meaning when it comes to tech truck rolls. For businesses, each roll can cost anywhere from $150 to over $1000, depending on the complexity of the issue and the distance traveled. These costs can quickly add up, especially for companies with widespread operations.
For consumers, while the immediate cost might be absorbed by their service provider, it ultimately reflects in their bills. This financial impact has spurred a industry-wide push for alternatives, driving innovations in remote diagnostics and self-service options.
“Every avoided truck roll is a win-win for both the company and the customer. It means faster resolution times and lower operational costs.” – Sarah Chen, Operations Manager at TechSolve Inc.
The Tech Truck Roll Process: A Step-by-Step Breakdown
- Issue Identification: The problem is reported and logged into the system.
- Remote Troubleshooting: Support staff attempt to resolve the issue without dispatching a technician.
- Scheduling the Roll: If remote efforts fail, a truck roll is scheduled based on priority and technician availability.
- On-site Diagnosis: The technician arrives and assesses the situation firsthand.
- Problem Resolution: Using their expertise and equipment, the technician works to solve the issue.
- Follow-up and Documentation: The resolution is documented, and follow-up steps are communicated to the customer.
This process, while seemingly straightforward, involves a complex orchestration of resources, scheduling, and expertise to ensure efficient resolution of technical issues.
Pros and Cons of Tech Truck Rolls
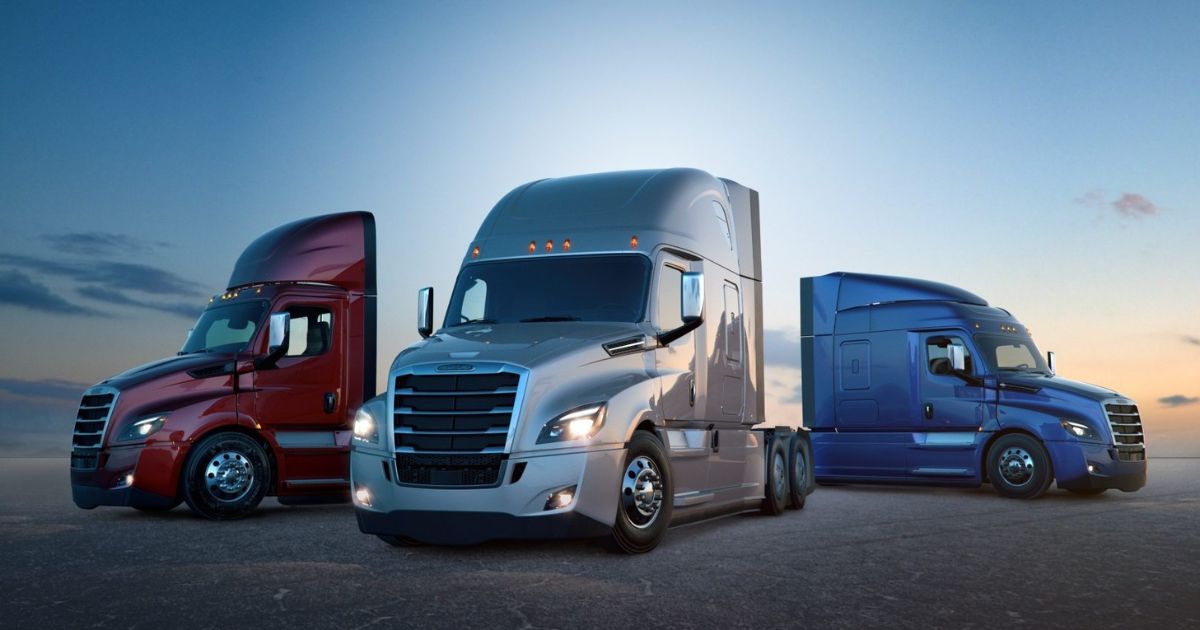
The Upside
- Face-to-face problem solving: Nothing beats having an expert on-site to tackle complex issues.
- Handling complex issues: Some problems simply require hands-on intervention.
- Customer satisfaction boost: The personal touch can significantly improve customer perception and loyalty.
The Downside
- Time-consuming: From dispatch to resolution, truck rolls can take hours or even days.
- Expensive for companies: The costs associated with maintaining a fleet and skilled workforce are substantial.
- Scheduling challenges: Coordinating between technician availability and customer schedules can be a logistical nightmare.
The Future of Tech Truck Rolls
As we peer into the crystal ball of tech support, several trends are shaping the future of truck rolls:
- Remote diagnostics and IoT: Smart devices are increasingly capable of self-diagnosing and reporting issues, potentially reducing the need for physical inspections.
- AI and predictive maintenance: Machine learning algorithms can predict failures before they occur, allowing for preemptive fixes.
- Virtual reality and augmented reality: These technologies could allow remote experts to guide on-site technicians or even customers through complex repairs.
While these advancements might reduce the frequency of truck rolls, they’re unlikely to eliminate them entirely. There will always be situations that require the human touch and expertise that only an on-site visit can provide.
Read This Post: A Tech Motorsports Return Address
Alternatives to Tech Truck Rolls
In the quest to minimize costly truck rolls, companies are exploring various alternatives:
- Self-service options: Comprehensive online guides and troubleshooting tools empower customers to solve issues independently.
- Advanced remote support tools: Screen sharing and remote access software allow technicians to diagnose and fix problems from afar.
- Modular equipment design: Easy-to-replace components can be shipped directly to customers, reducing the need for on-site technician visits.
Tips for Consumers: Making the Most of a Tech Truck Roll
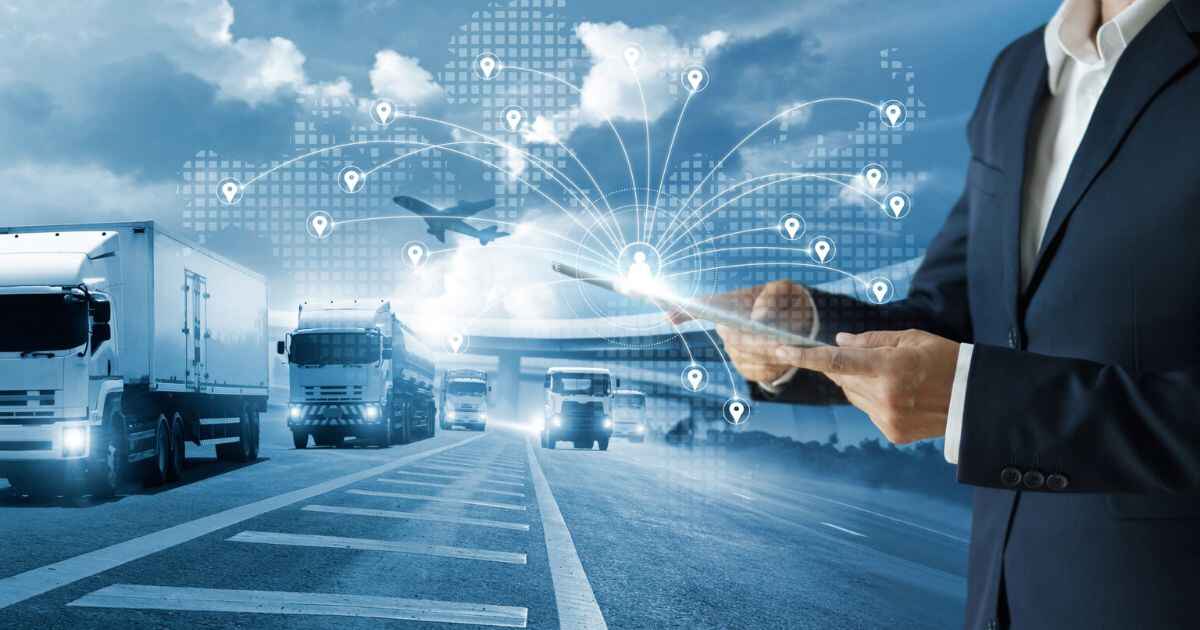
If you find yourself on the receiving end of a tech truck roll, here are some tips to ensure a smooth experience:
- Prepare ahead of time:
- Document the issue thoroughly
- Clear access to all relevant equipment
- Ensure someone knowledgeable about the problem is present
- Questions to ask the technician:
- What was the root cause of the issue?
- How can I prevent this from happening again?
- Are there any warning signs I should watch out for?
- Follow-up measures:
- Take notes during the visit
- Implement any recommended changes or upgrades
- Keep track of the resolution for future reference
By being proactive and engaged during a truck roll, you can not only ensure a swift resolution but also gain valuable insights to prevent future issues.
FAQs
What exactly is a tech truck roll?
A tech truck roll refers to the dispatch of a technician to a customer’s location to resolve a technical issue that couldn’t be fixed remotely. It involves sending a skilled professional with specialized equipment to diagnose and repair problems on-site.
How much does it cost?
Typically $150-$1000+, depending on the issue’s complexity and travel distance.
When is it needed?
For persistent outages, hardware failures, or complex installations that require hands-on expertise.
Can’t all tech issues be solved remotely now?
No, some problems still need on-site diagnosis and repair with specialized tools.
Are there alternatives?
Yes, like advanced remote support, self-service options, and IoT diagnostics, but truck rolls remain essential for complex issues.
Conclusion
Tech truck rolls remain a vital component of the tech support ecosystem, bridging the gap between remote assistance and hands-on problem-solving. While the landscape of tech support is evolving with new technologies and approaches, the fundamental value of having a skilled technician on-site continues to hold true.
As consumers and businesses alike navigate an increasingly complex technological world, understanding the role, process, and implications of tech truck rolls can lead to better-informed decisions and more efficient problem resolution. Whether you’re a tech enthusiast or simply someone who relies on technology daily, appreciating the intricacies of this often-overlooked service can provide valuable insights into the infrastructure that keeps our digital lives running smoothly.
So the next time you see a service van rolling down your street, you’ll know there’s more to it than meets the eye – it’s a crucial cog in the machine that keeps our connected world spinning.